The Catalysing Effect of ERP Systems on Production in Manufacturing
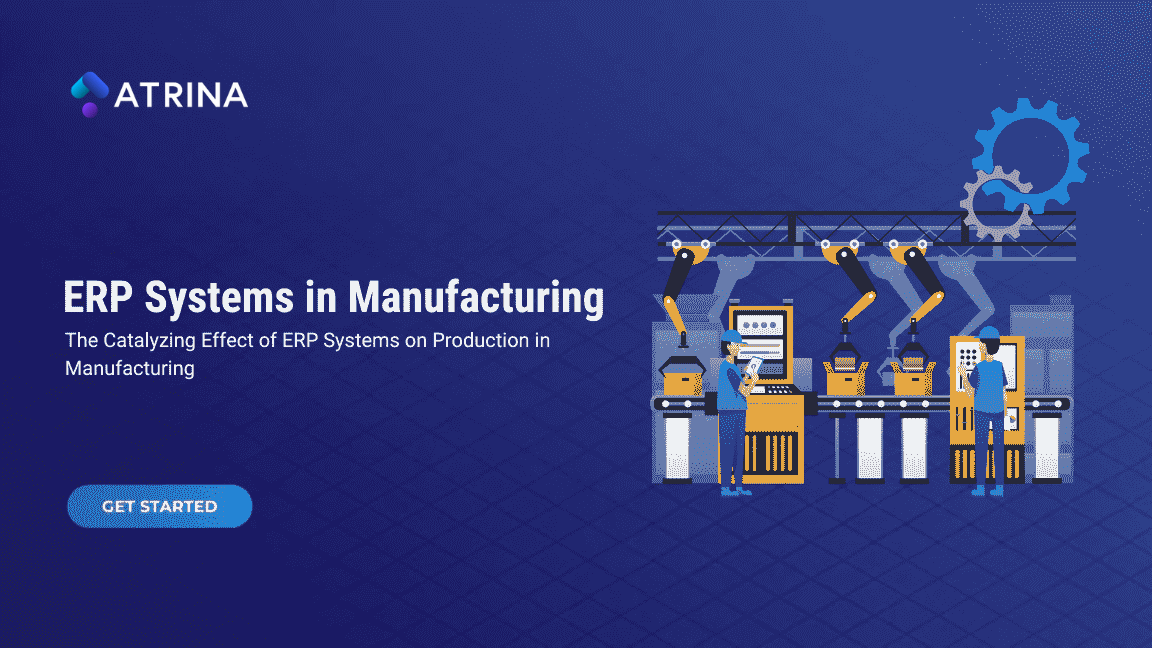
“ERP is first an attitude; second, a process, and only third, a set of tools.” – Alexis Leon.
The industrial landscape is expanding fast, and staying a step ahead of the rest is vital, especially for the manufacturing segment that has always been demanding, fast-moving, and innovative. There is a need for the industry to remain agile and efficient at every step of its working process.
And for that to happen, nothing better or recommended than an effective Enterprise Resource Planning (ERP) system that has formed the fundamental building block for industries worldwide. Some popular statistics say that manufacturing is the main user of ERP, with 33.66%, and the rest follow. In the manufacturing industry, ERP systems are used to manage 43% of the data.
ERP systems have transformed the operations of manufacturing segments through their integrated and comprehensive solutions. The extent to which ERP has influenced production planning, monitoring, and control has been rewarding.
This article explores the impact of ERP on manufacturing units and especially the entire production process, which forms the heart of this domain. Before we plunge into details of how ERP affects the production process, let us quickly have a look at the salient features of manufacturing ERP systems.
Manufacturing Enterprise Resource Planning System – An Overview
Enterprise resource planning (ERP) is the integrated management of main business processes, often in real-time and mediated by software and technology.
When it comes to the manufacturing landscape, a centralized manufacturing ERP system assists manufacturers in automating and managing their daily activities like production, inventory, financials, orders, etc, in an effective manner. Offering real-time information helps the units to make business decisions with foresight and precision. It becomes easy for manufacturers to keep monitoring inventory levels and production processes, respond quickly to market changes, and identify futuristic trends and patterns for better business outcomes.
The types of organizations that need manufacturing ERP systems are large-scale manufacturers, SMEs, process manufacturers, contract manufacturers, etc. Users who leverage manufacturing ERP are product manufacturers, supply chain manufacturers, quality control personnel, inventory managers, finance and accounting personnel, etc.
Manufacturing ERP helps industries overcome challenges such as
- The complexity of production and supply chain procedures
- Inefficient production processes
- Problems with quality control
- Adherence to regulatory requirements
- Higher costing factors
- Absence of real-time transparency
Salient Advantages of Implementing an ERP Solution
- Better and futuristic forecasting and visibility
- Enhanced data security and quality control
- Improved supply chain and production management
- Automation of business processes and workflows
- Savings on costs, time, and data
- Seamless collaboration between systems and departments
- Augmented visibility into the process flow
- Increased demand monitoring and planning
- Centralised data analysis and collection
- Minimal data redundancy
- Accurate planning and forecasting
- Better financial management
- Brighter and faster business decisions
- Clearer competitive edge
How is ERP Influencing Production in Manufacturing Units?
- Efficient Production Planning, Monitoring, Scheduling and Control
ERP integrates and streamlines the entire process of production starting from procurement of raw materials to the end delivery of products. It automates tasks, offers transparent visibility, and optimises the production planning process to avail best of results. It cohesively, gets together various functionalities in the business, acting as a centralized repository.
Information flows smoothly across different stages of production planning, collaborating within departments, enabling smooth supply chain management. It offers a comprehensive view of the production planning information with effective monitoring and control. ERP offers details about resource utilization, production schedules, client demands, inventory levels, and market trends that help stakeholders make the right decisions at the right time.
ERP also offers insightful reports and dashboards that are competent to offer a holistic view into the production capabilities and, thereby, make optimal decisions on the go. This helps in finding anomalies on time, extracting trends, and finetuning the entire production procedure.
ERP in production units offers instantaneous updates on the status of orders, helping manufacturers view the orders in progress, whether on time or delayed. Even machine utilization can be monitored, and if not utilized properly, it can either be assigned for some other task or can be repaired if needed.
- Timely Quality Monitoring and Control
ERP systems can work wonders in ensuring that all involved systems maintain the needed levels of quality. Ensuring that all quality control mechanisms are followed and in place and necessary results are obtained on a regular basis ensures a controlled quality mechanism. There are dedicated quality control modules in the ERP system that take care of the production schedules, output, and whether they comply with the regulatory requirements or not.
These modules ensure real-time surveillance and testing of products as they pass through the different stages of production. This ensures the timely detection of errors and their solutions. It also helps in needed documentation and traceability of quality control procedures with which backtracking becomes easier and more effective.
- Automation of Work Orders
ERP systems help in creating and managing work orders in an automated manner, working out in detail the steps needed to create a product. Based on the orders generated or the forecasting of sales, it generates work orders, lessening the manual intervention and time spent on the same.
These work orders also specify the resources that could be needed to fulfill the production needs, including equipment details, material required, and labor needs. It enables effective planning of resources and thereby ensures proper access to resources and emphasis on timely delivery.
- Simplification of Production Schedules
Since ERP systems have a stringent impact on production management and control, they can very well simplify the different production schedules. It helps in adapting to new situations and enhances production efficacy, leading to simplified process execution.
It reduces wastage, increases performance, manages complicated processes with ease, and hence leads to a timely and regular delivery schedule. Management efficacy also improves with a transparent view of all production schedules.
- Generation of Timely Production Reports and Dashboards
With all the above contributions of ERP to production-related activities, the ideal output is through the generation of regular and needed reports and dashboards. These reports prove to be a transparent face to what is happening, and it is accessible at the right time, at the right place with the right format, for the right audience.
Everyone is happy: the production workers, the customers, the top management, and the end users. Viewing what is actually happening can be the best output of any software solution.
Final Thoughts
It is interesting to see how Manufacturing ERP systems are showing contributions to great futuristic trends like Industry 4.0, IoT integration, Big Data analytics, cloud-driven services, AI and ML, Natural Language Processing, predictive maintenance, remote monitoring through mobile devices, etc.
Selecting a reliable and experienced ERP solution provider is vital for its implementation success in the manufacturing industry. ERP system is a complicated process that needs careful planning and execution. Hence, some of the steps to be followed are defining the basic purpose, selecting the ideal vendor, planning for detailed implementation, and training and orienting the taskforce.
Important factors while choosing the right ERP system and vendor are integration competencies, industry fit, customization capabilities, user friendly interface, scalability, reputation, and cost analysis.
ERPNext: Your Perfect Manufacturing Partner
As a certified ERPNext implementation partner, Atrina can help you with ERPNext development, an open-source ERP system designed for the specific needs of manufacturers. Our team can customize ERPNext to optimize your production planning, inventory management, and quality control, ensuring efficient operations and a competitive edge. Contact us today to discuss your manufacturing challenges and explore how ERPNext can empower your business.